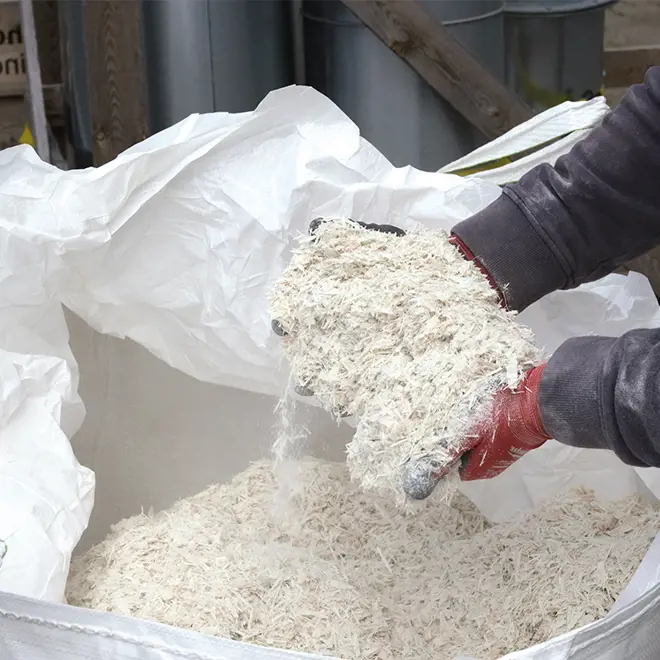
In collaboration with glass fibre producer 3B-Fibreglass, the DecomBlades partners are pursuing a circular route for the glass fibre from decommissioned wind turbine blades – a route that has the potential to off-take the coming years’ waste stream.
The DecomBlades consortium has teamed up with glass fibre producer 3B in launching a ground-breaking commercial-scale experiment in 3B’s plant in Birkeland, Norway to prove that it is both possible and environmentally viable to use pyrolysis as part of the production process of high-quality glass fibre from old wind turbine blades. This is a crucial step in the consortium’s work aiming to establish value chains that can ensure the sustainable recycling of wind turbine blades.
The DecomBlades project’s overall aim is to establish the basis for sustainable, cost-efficient, and viable value chains for recycling of wind turbine blades.
The innovation project is funded by Innovation Fund Denmark and is a collaboration between MAKEEN Energy, LM Wind Power, Siemens Gamesa, Vestas Wind Systems A/S, Ørsted, Technical University of Denmark (DTU Wind and Energy Systems), University of Southern Denmark (SDU), HJHansen Recycling, FLSmidth, and Energy Cluster Denmark.
Currently, a lot of material in decommissioned wind turbine blades is either sent to landfill or is incinerated for cement production, substituting other waste streams for heating. As more and more wind turbines are put up across the world, the challenge is to find sustainable and feasible methods of recycling the materials.
3B and DecomBlades’ current experiment focuses on pyrolysis as a means to prepare fibres for remelting. Pyrolysis is a process of exposing materials to high heat in an oxygen-free environment and is used to separate the materials. The materials are processed and then used in new applications.
The ambition for the DecomBlades partnership is to demonstrate the feasibility of re-melting recycled glass fibre to increase circularity and determine the greenhouse gas emissions impact.
The process explained
The method that DecomBlades aims to demonstrate, allows the glass fibre to separate from other ingredients such as resin, coating, core material, adhesive, and metals. The technical solution for the pyrolysis process has been developed by a team of engineers at MAKEEN Energy.
Irene Bach Velling Villadsen, MAKEEN Energy’s Project Manager for the DecomBlades project, explains the process:
“We take 2 old wind turbine blades, shred them, pyrolyze them, sort out any metal, and mill the remaining material into a powder. Then 3B will substitute some of the virgin raw material in the glass fibre manufacturing process with this powder. In the trial we aim to prove that it is possible to substitute 5 % of the raw material with this powder and remelt it into glass fibre that is just as good as glass fibre produced only from virgin raw materials. Not reducing the material quality is key to enabling a true circular industry where resources can be reused indefinitely.”
MAKEEN Energy will manage the joint task in the project. They will also conduct the pyrolysis process in their own equipment for continuously processing the six tonnes of End-of-Life wind turbine blades donated by LM Wind Power that will form the basis for the trial. The project has partnered with the glass fibre producer 3B-Fibreglass, which will carry out the trial in its production plant in Norway. 3B will perform the remelting of the powder and test the quality of the glass fibre produced. The Technical University of Denmark (DTU) will perform third-party tests and verification of the properties of the glass fibres with recycled content.
Trusted partners
Wind turbine blade manufacturers Siemens Gamesa and LM Wind Power will evaluate the results of the trial and determine the feasibility of employing recycled content in new wind turbine blades. Provided that glass fibres produced with recycled content can meet the same standards as glass fibres made from 100% virgin raw material, the companies would be on the way to proving that full circularity – from fibre to fibre without losing quality – is achievable.
3B and the consortium have already had good results from lab-scale analyses.
At Siemens Gamesa we are working towards fully recyclable turbines, and we think this proof-of-concept is very interesting and a promising route for closed-loop recycling of the glass fibre in our products. We are happy to work with trusted partners on this project.
Implications for the industry
By recovering the glass fibre in a quality that is equal to virgin material, the project also aims to reduce the need for extraction and processing of the raw materials used in glass fibre production. An initial Life Cycle Assessment (LCA) shows that in terms of total environmental impact, pyrolysis of used materials is a feasible alternative to mining and pre-processing the silica, limestone, dolomite, and kaolin that are typically used to make glass fibre.
If the method is implemented, the DecomBlades consortium estimates that substituting between 1-5% of raw materials in the production in Europe with cleaned glass fibre from end-of-life blades is currently enough to handle all the material from Europe’s annual number of decommissioned blades.
John Korsgaard, Senior Director, LM Wind Power and Chair of DecomBlades Consortium, states:
“Today, it is an industry challenge to find viable ways to use recycled materials from decommissioned wind turbine blades in a sustainable, cost-efficient manner, in addition to incorporating them into suitable resource streams. Recycling end-of-life materials like glass fibres from decommissioned blades through processes like remelting and reusing them to build new products, is an effective route to ensure resource utilization and circular economy of raw materials. To support the much-needed transition to a circular economy, recycling technologies like pyrolysis need to be sustainable to address the incoming volumes of decommissioned blades. And for that we need established value chains and facilities which are not just limited to taking end-of-life blade wastes, but waste from other composite industries as well,”.
About DecomBlades
3B and DecomBlades’ experiment will continue until the end of December 2023.
More information about the project can be found at www.decomblades.dk