Knowledge Centre
A variety of climate conditions can impact the safety and lifespan of LPG cylinders. Factors such as humidity, salinity, extreme temperatures, and other environmental elements can influence their safe operation and filling. Rust is a common problem faced by LPG cylinders in harsh climates. Additionally, harsh climates can affect how cylinders are handled, accelerating wear and tear. At MAKEEN Energy, we have developed solutions to address some of the challenges faced by LPG cylinders in demanding environments.
Protecting cylinders in humid conditions
When exposed to humid conditions, LPG cylinders are at risk of rust and corrosion, which can compromise their integrity and lead to leaks or explosions. There are many solutions to help protect cylinders in these conditions. The preparation process of the surfaces of the cylinders is vital. Corrosion classes are an important consideration when selecting the correct finish for metal products. These environmental categories are measured from low to high with C1 representing internal, dry environments and C5 representing harsh environments such as coastal areas with high salinity. In C5 environments the risk of corrosion is very high and the recommendations for surface treatment of cylinders differ. Most options for the surface treatment for cylinders must be carried out in non-hazardous areas and involve several steps. Below, we will outline some of these options for you.
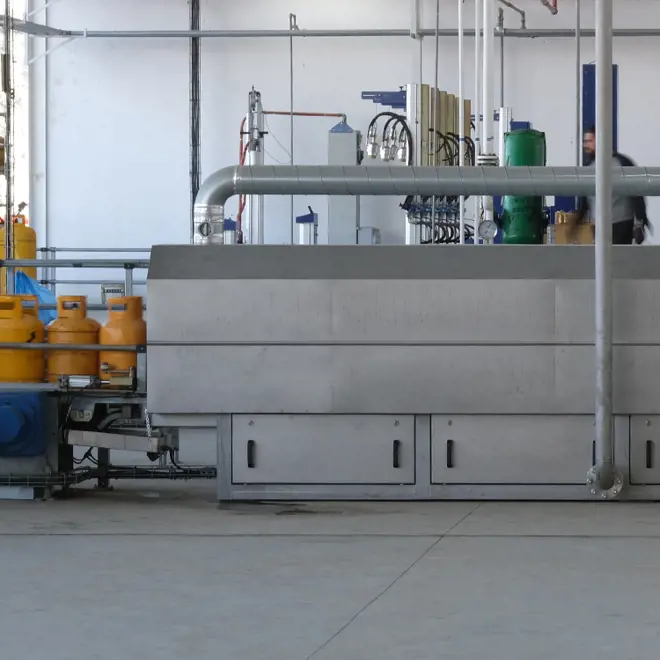
Cleaning of cylinders surfaces
Before any surface treatment of cylinders, it is essential to ensure that cylinders are cleaned and free of rust and other contaminants. If protective coatings are applied to an unclean cylinder surface, residual rust can continue to corrode the steel beneath protective layers. There are various cleaning options available to prepare cylinders effectively.
Cylinder washing
Cylinder washing is an optional cleaning step in surface treatment that can be performed in non-hazardous areas. Washing machines fully submerge cylinders to remove imperfections, enhancing appearance and hygiene while potentially reducing the need for frequent maintenance. Various in-line systems can be installed to integrate cylinder washing.
Shot blasting
Shot blasting is the most effective method for removing rust and other irregularities in the metal of the cylinder surfaces. This process uses high-velocity abrasives, such as steel grit or sand, propelled by pressurised air or centrifugal force in a secured blasting chamber. Shot blasting removes rust and contaminants while roughening the surface of the cylinder, significantly enhancing coating adhesion. Shot blasting is foundational for long-lasting protection and is the most effective method to ensure cylinders are thoroughly clean before coating application.
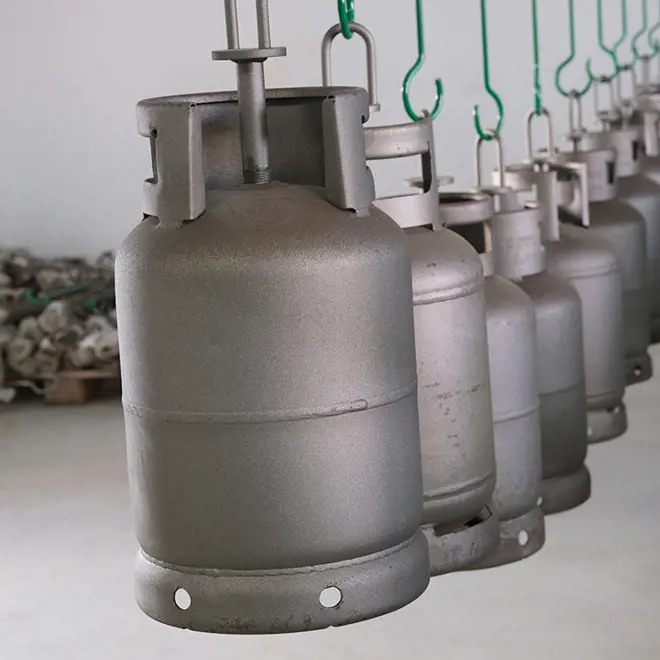
Pretreatment
Pretreatment methods can provide base layers that protect cylinder surfaces and enhance the effectiveness of topcoats applied afterward. Several pretreatment options are available to suit different needs.
Metallization
For the most effective protection in harsh conditions, pretreatment with metallization is recommended. This intense process involves spraying melted metal, typically zinc, onto the cylinder surface, where it cools and solidifies to form a strong protective layer. Zinc has anti-corrosive properties. The metallized coating serves as a sacrificial layer, meaning it will corrode before the steel underneath if rust is present. Multiple layers can be applied if needed. In C5 environments, this solution is best. This solution is the most expensive cylinder pretreatment method but is also the most cost-effective in the long, as it significantly extends the lifespan of cylinders.
Powder Primer
A powder primer containing zinc can be applied as pretreatment for cylinders to guard against rust and corrosion. Applied with spray guns, the powder is evenly distributed across the cylinder surface and then heated in an oven. The heat melts the powder, bonding it firmly to the cylinder’s surface. Once the cylinder leaves the oven, it cools, and the powder coating hardens to form a durable, corrosion-resistant layer to protect against environmental factors.
Wet Primer
A wet primer can also be applied as pretreatment and is required if applying a wet paint topcoat. This is a common and less expensive method that offers basic protection against rust and corrosion. This wet primer is a thick paint with a high pigment-to-solvent ratio. This provides long-lasting protection against moisture in mild environments. Wet primer is less expensive than other pretreatment options and can be sufficient in mild environments. Harsh climates with extreme humidity typically require more robust pretreatments than wet primer, such as metallization or powder primer, for optimal protection.
Epoxy coating
Epoxy coatings can also be applied as a form of pretreatment for cylinders. This can provide effective protection against rust, corrosion, and chemicals, creating an impermeable barrier that reduces the need for frequent maintenance and reapplication. However, epoxy requires a two-part mixing and curing process that requires precision, or the epoxy could cure too hard potentially interfering with cylinder components, such as nozzles. Epoxy coatings offer a long-term, cost-effective solution due to their durability and reduced maintenance needs. With ongoing innovation to refine the application process and address compatibility with cylinder components, epoxy coatings have the potential to become a viable option for protecting cylinders in harsh climates.
Topcoats
Powder paint topcoat
A powder paint topcoat can provide effective protection for cylinders in harsh climates. This topcoat of powder paint does not include zinc like the powder primer that can be used for pretreatment. The topcoat is applied to the cylinder with spray guns to evenly distribute the powder paint across the cylinder surface, the cylinder is then treated with heat and the topcoat layer is melted into the cylinder surface resulting in a hardened layer of protection from moisture and corrosion. This can be applied atop a powder primer or metallized coating.
Wet Paint Topcoat
Wet paint can be applied as a topcoat following a wet primer and is often a more affordable option than powder paint alone. After application, wet paint requires several hours to dry, and many choose to install a drying oven to expedite the process, adding to the overall cost of the process. While wet paint provides adequate protection in some environments, harsher conditions with high humidity and salinity require more durable topcoats, such as powder paint, for effective, long-term protection.
Our Recommendation
Among the options for protecting LPG cylinders in harsh climates, we recommend starting with shot blasting to thoroughly remove rust and clean cylinder surfaces. Following shot blasting, a zinc powder primer as a base layer with a powder paint topcoat offers a cost-effective, durable solution against rust and corrosion.
For maximum protection, especially in extreme conditions, metallization as a pretreatment provides the highest level of defence. Though it is the most expensive option, it remains cost-effective over time. For optimal results, combining metallization as a base layer with a powder paint topcoat delivers the strongest shield against persistent rust and corrosion in harsh conditions, extending the lifespan and durability of LPG cylinders.
It's also possible to begin with select treatments, such as a powder paint topcoat, which may provide sufficient protection in less extreme environments. Then allow for the addition of further surface treatments as needed. Leave room in the treatment areas for the installation of further processes in the future.
Application of surface treatment in hazardous areas
Most surface treatments for cylinders must be applied in non-hazardous areas. However, cosmetic paint is an exception and can be applied in hazardous areas, offering a low-cost option for cylinder surface treatment. With a low solvent-to-pigment ratio, cosmetic paint provides only minimal protection against rust and other elements. This wet paint can mask existing rust and surface imperfections, although these flaws still exist beneath the paint and may be visible as bulges. Cosmetic paint can improve the cylinder appearance to a degree. This is typically applied in a single layer and dries quickly. However, frequent reapplication is needed to maintain its appearance and limited protective benefits.
Download the e-book
Download the e-book and learn how to protect your cylinders and extend their lifespan, even in the harshest climates.
Click below to get your free copy and put these insights to work!