MAKEEN Energy Commitments
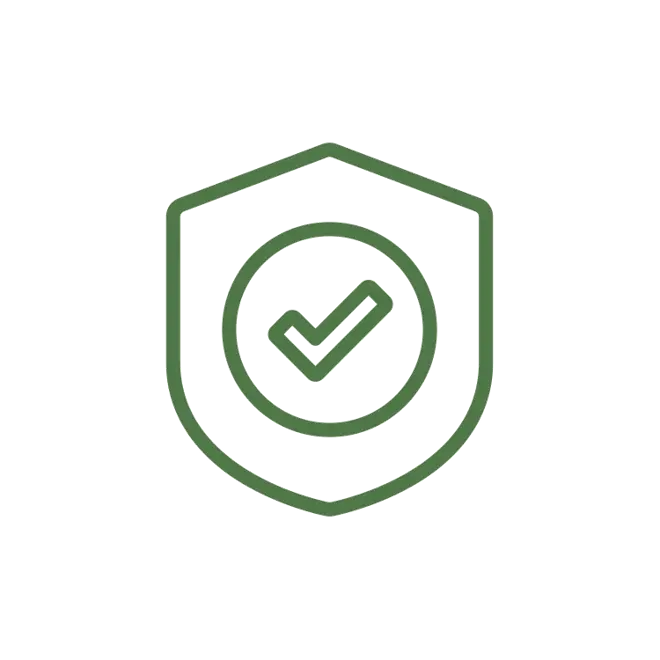
Safety comes first – always
As a company that develops, manufactures, and operates equipment that in many cases is located in hazardous zones or uses hazardous materials, we can and will not compromise when it comes to safety. And that extends to our own internal working procedures as well.
Reporting in Sri Lanka
As an ISO 45001 certified company, MAKEEN Energy Sri Lanka has committed to upholding the international standard for health and safety, ensuring a safe environment for our employees. MAKEEN Energy Sri Lanka proactively utilize a risk management reporting tool to assess previous incidents to improve safety in the work environment.
We have been operating without any lost time injuries (LTIs) for over three consecutive years, while reporting an average of approximately 15,000 work hours a month.
As per industry standards, this means our LTIFR (lost time injury frequency rate) is 0, reflecting our safety culture and commitment, which we are very proud of – safety will always be our number one concern.
For the future, this reporting tool is to roll out globally, ensuring a clear overview of incidents, making it possible to prevent any safety hazards.
Note: Lost time injury frequency rate (LTIFR) is defined as the ‘number of lost time injuries’ for one million work hours for a given accounting period.
The Working Environment Committee
At MAKEEN Energy Denmark, we have an active Working Environment Organization, ensuring that the health and safety of our colleagues is never compromised.
The Working Environment Committee meets on a quarterly basis to identify and resolve potential issues, review incidents, plan emergency responses, and eliminate or reduce physical and psychological risks in line with Danish Working Environment Authority guidelines. All employees are encouraged to share their ideas or concerns with committee members so we can continuously enhance our working environment together.
Safety inspections
On July 24, 2024, MAKEEN Energy Denmark underwent an inspection from the Danish Working Authority. The visit was with the objective of auditing how APV’s (Workplace assessments) are being done and the psychological working environment in MAKEEN Energy. We are very proud that the Danish Working Environment Authority had no remarks.
You may also like ro read
MAKEEN Energy's commitments