Plastcon – Plastic waste conversion
Through our patented technology, Plastcon is able to recycle plastic waste over and over again. We break down plastics to their molecular level, unlocking valuable resources for new products.
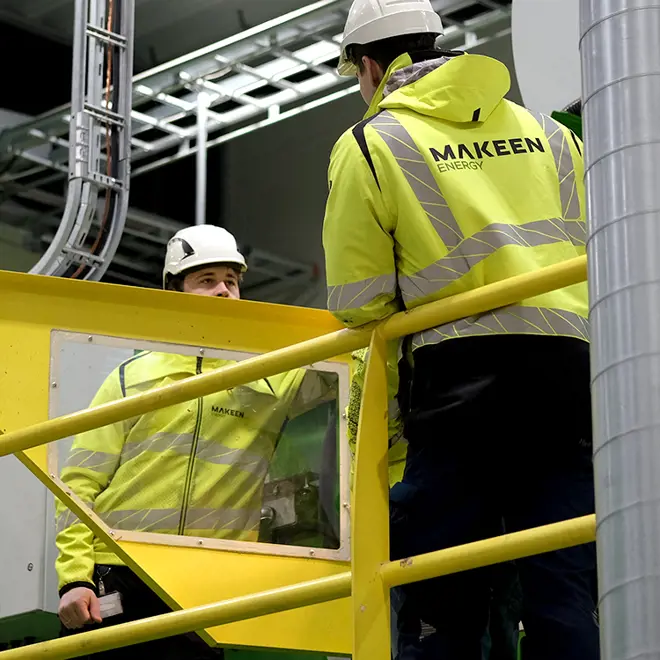
Technology at our core
Our team boasts some of the most skilled engineers, specialising in mechanical engineering, process design, and project management. This talented and competent team covers all facets of the Plastcon process, ensuring that each stage of the project is handled with the utmost expertise and precision.
One of our key strengths at MAKEEN Energy is our hands-on experience in operating the plastic waste conversion plants we build. This direct involvement gives us an in-depth understanding of day-to-day operations and allows us to provide valuable feedback to our design department. Such a feedback loop is crucial for the continuous development and improvement of our technologies, ensuring that each project is not only successful but also leads the way in innovation and efficiency.
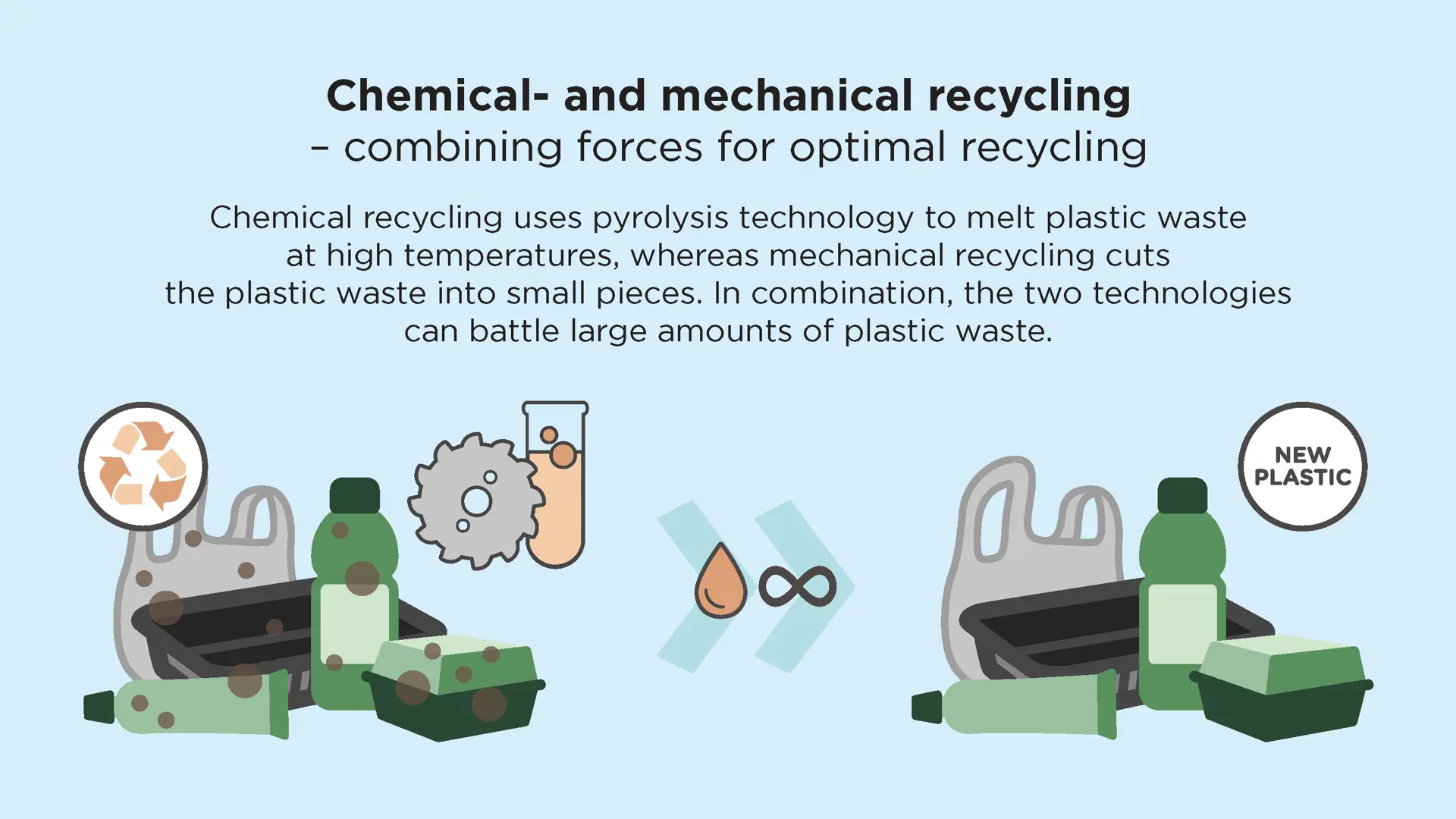
Mechanical and chemical recycling each play a distinct role in the overall strategy for managing plastic waste. Mechanical recycling is efficient and energy-efficient for processing plastics that are uncontaminated and uniform in composition, as it involves cleaning, sorting, and remelting the materials.
In contrast, chemical recycling is an advanced process that breaks down plastics into their molecular components. This method is particularly effective for handling plastics that are not suitable for mechanical recycling due to contamination or complexity. It allows for the recovery of raw materials, which can be used to produce new plastic products of high quality - such as medical equipment or food packaging, which is not possible with mechanical recycling.
Both mechanical and chemical recycling are necessary when creating a more robust and versatile recycling system. By utilising both, not only maximises the recycling rates of various types of plastic waste but also contributes to resource conservation and working together on the reduction of plastic waste.
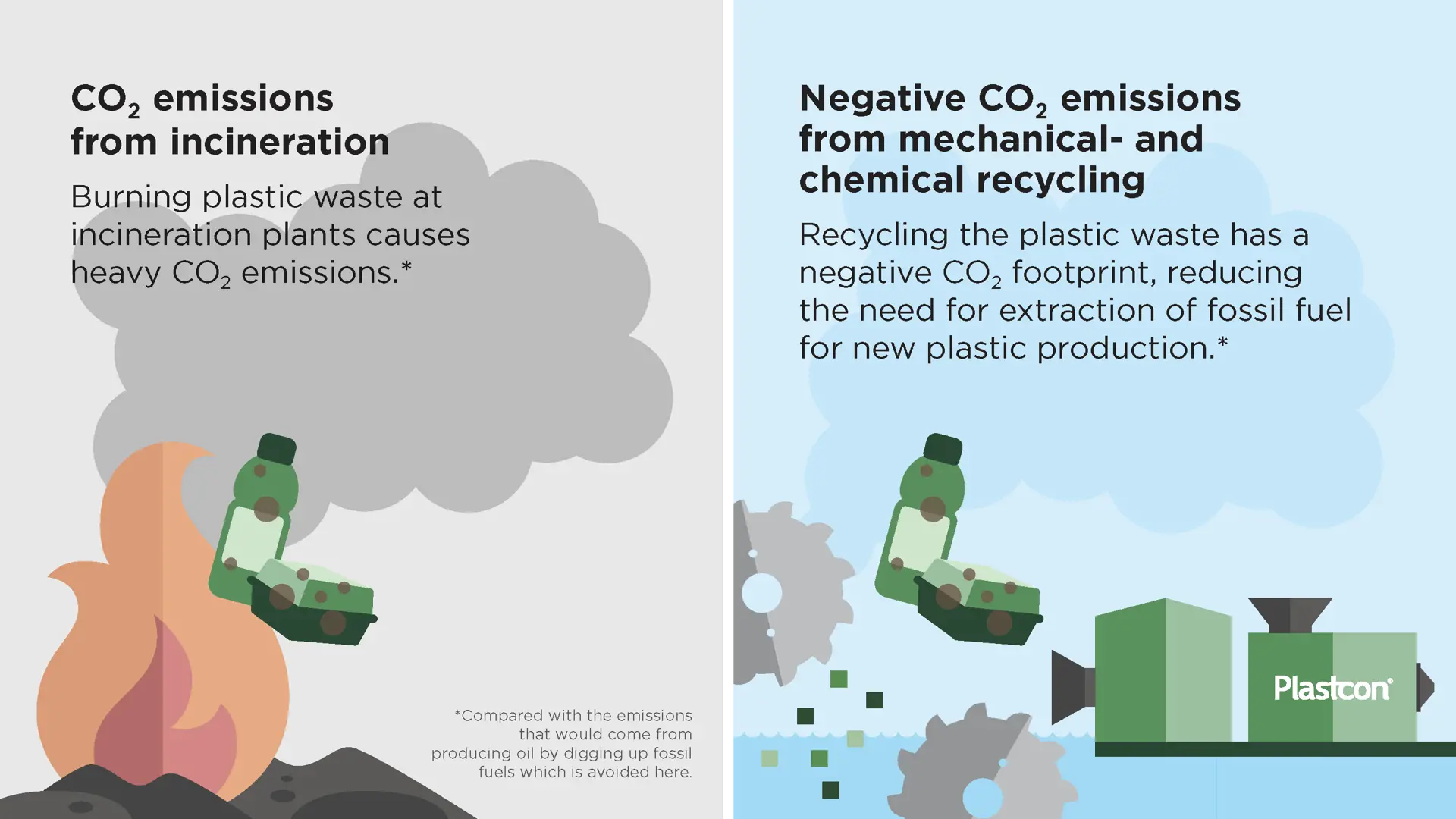
5 benefits of Plastcon
Solving part of the plastic waste problem
Plastcon can help turn the tide on the global and growing issue with plastic waste pollution by converting plastic waste into useful resources.
Never without safety
At MAKEEN Energy, safety is number one priority. This is also the case for Plastcon. We have developed extensive safety procedures and protocols, ensuring operations run smoothly. The plant is highly automatised, reducing the risk of errors or accidents.
High quality oil for high quality products
Plastcon chemically recycles plastic waste, which ensure a very high quality of pyrolysis oil. As a result, the oil can be used for new plastic products, where the quality cannot be compromised, such as food packaging and medical equipment.
Teaming up with mechanical recycling
While Plastcon can handle a large variety of plastic types, not all plastic waste makes oil with the desired quality. As the world is currently overflowing with plastic waste, chemical recycling cannot stand alone. The problematic plastic waste that cannot be used for high quality oil, can be mechanically recycled for other purposes. In short, the two recycling methods complement each other towards a mutual goal.
Modularise to your desire
The Plastcon system is entirely modular. This means that the system is built in separate sections, making it possible to customise a solution and scale to purpose.