Plastcon – Plastic waste conversion
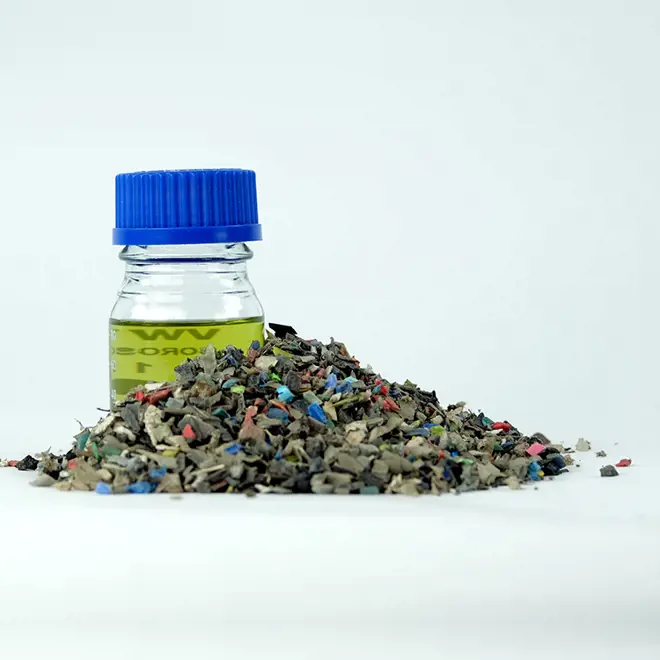
An important resource
Since the mass-production of plastic took off in the 1940’s, plastic has transformed our lives to the point that it is woven into the fabric of modern society.
Due to plastic's versatility, durability, and cost-effectiveness, you find plastic in all sectors, from healthcare and transportation to food packaging and retail. Lighter vehicles made possible by plastics reduce fuel consumption and emissions. Sterile plastic medical equipment has revolutionised healthcare, preventing infections and saving countless lives. Let's not forget the convenience of packaging, preserving food, and reducing waste. It is undeniable that plastic has a vital function in today’s society and made basic amenities available to a much wider portion of the world’s population.
But while the world embraced the many qualities of plastic, we forgot to address one critical concern:
What do we do with the plastic after it has been used?
Innovation within the industry has led to significant strides in developing recyclable and even biodegradable plastics. It's essential to remember that when used responsibly and with a well-structured waste management system, plastics can coexist with a healthy environment. The key lies in responsible consumption, recycling, and innovation.
With decades of engineering experience, we challenged ourselves to another venture – to create a sustainable and circular life cycle of plastic waste and closing the gap.
Handling plastic waste today
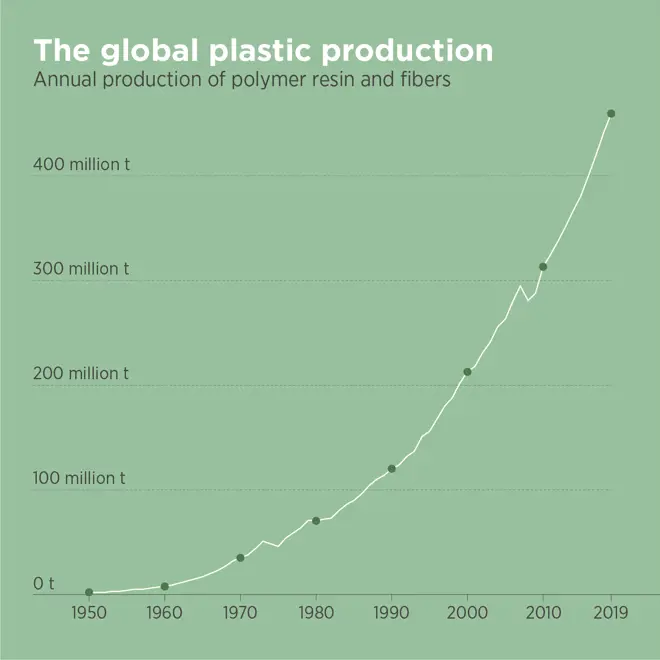
The global plastic production
Between 1950 and 2017, an estimated 9.2 billion tonnes of plastic were manufactured. Over half of this quantity was produced after 2004. In the year 2019 alone, the production of plastic amounted to 400 million tonnes. Should the current demand for plastic persist, projections indicate that the yearly worldwide production of plastic could surpass 1.1 billion tonnes by the year 2050.
https://ourworldindata.org/grapher/global-plastics-production
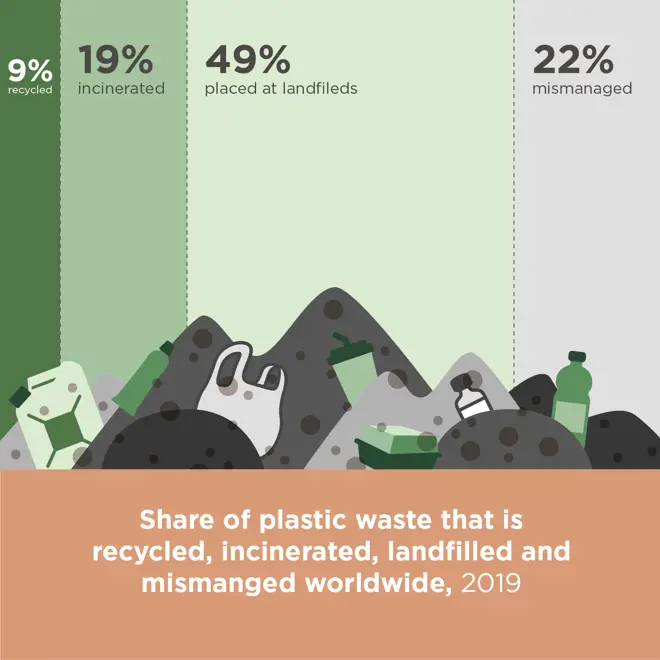
The fate of plastic waste
As of 2019, merely 9% of plastic waste globally is recycled. A lot of plastic waste ends up in landfills, oceans, and in nature, which causes damage and pollutes our planet, but is also harmful to animal life.
And with the increasing production of plastic, it is crucial to recycle and reuse the resources we already have, without compromising on the functionality.
Our Plastcon plant exemplifies our commitment to addressing the challenge of plastic waste. Developed by our team, this plant leverages advanced pyrolysis technology to efficiently process plastic waste with our circular technology, maintaining the quality of the material.
As global plastic production continues to rise and its use remains integral to modern society, the role of effective recycling solutions like Plastcon becomes crucial. Considering that only a small percentage of plastic waste is currently recycled, the need for improved recycling methods is evident. Plastcon responds to this need, offering a practical solution to reduce pollution and its harmful consequences for ecosystems and wildlife.